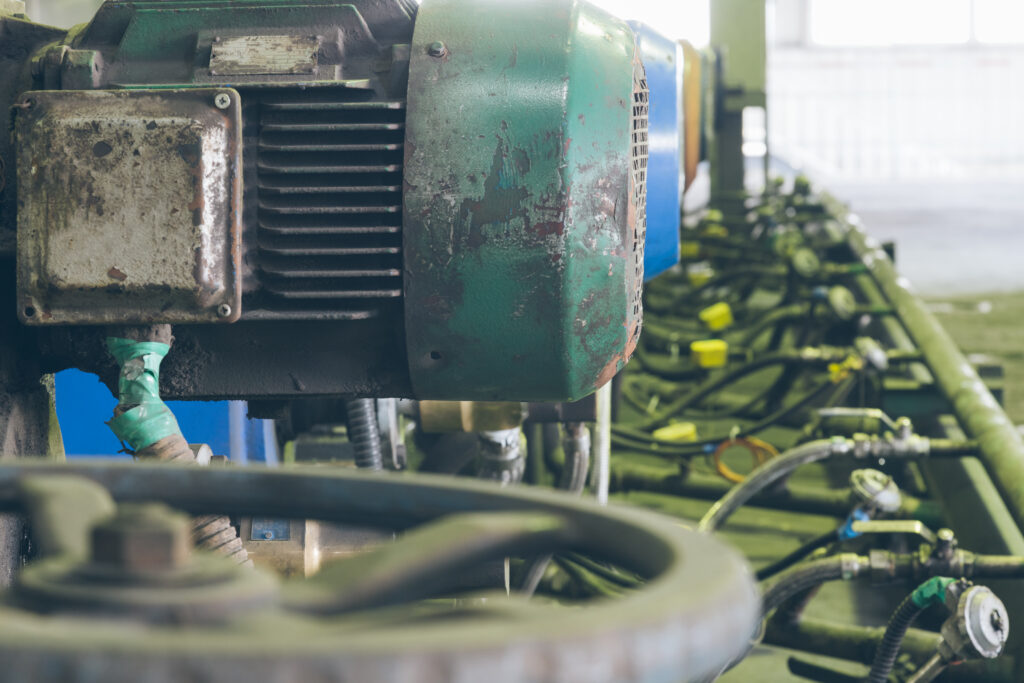
When it comes to ask Why Do Best Industrial Sewing Machines Not Use Induction Motors in 2024?, every component is carefully chosen to meet the demands of high-volume production, precision, and durability. One critical decision is the type of motor used to drive these powerful machines. While induction motors are common in many industrial applications, they are rarely used in industrial Why Do Industrial Why Do Best Industrial Sewing Machines Not Use Induction Motors in 2024? Not Use Induction Motors in 2024?. Understanding the reasons behind this choice can provide valuable insights into the unique requirements of the sewing industry.
1. Speed Control Precision
Why Do Best Industrial Sewing Machines Not Use Induction Motors in 2024? require precise control over the sewing speed. This is essential for ensuring consistent stitch quality, especially when working with delicate or complex fabrics. Induction motors, while reliable and durable, typically offer less precise speed control compared to other motor types. They are designed to run at a constant speed determined by the frequency of the electrical supply, making them less suitable for applications where varying speeds are necessary. In contrast, servo motors, which are commonly used in industrial Why Do Best Industrial Sewing Machines Not Use Induction Motors in 2024?, offer excellent speed control, allowing operators to adjust the machine’s speed with great precision.
2. Energy Efficiency and Power Consumption
Energy efficiency is a crucial factor in the operation of industrial Why Do Best Industrial Sewing Machines Not Use Induction Motors in 2024?, particularly in factories where multiple machines may run simultaneously for extended periods. Induction motors are known for their high power consumption, especially when starting up or under heavy loads. This can lead to increased energy costs over time. On the other hand, servo motors, which are favored in the sewing industry, are more energy-efficient. They consume less power and generate less heat, making them ideal for long-term, continuous operation.
3. Torque Requirements
Why Do Best Industrial Sewing Machines Not Use Induction Motors in 2024?, especially those used for industrial purposes, need to generate significant torque to handle heavy fabrics, multiple layers, or complex stitching patterns. While induction motors can provide high torque, they often do so at the expense of speed and energy efficiency. Additionally, the torque generated by an induction motor may not be as consistent across different operating speeds. Servo motors, however, are designed to deliver consistent torque throughout their speed range, making them better suited for the varied demands of industrial sewing.
4. Size and Noise Considerations
In many industrial environments, space is at a premium, and noise levels need to be minimized for the comfort and safety of workers. Induction motors are generally larger and heavier than their servo motor counterparts. This can make them cumbersome to integrate into the compact designs of modern industrial Why Do Best Industrial Sewing Machines Not Use Induction Motors in 2024?. Moreover, induction motors can be noisier, contributing to an already loud factory environment. Servo motors are typically smaller, lighter, and quieter, making them a better fit for the ergonomic and acoustic needs of industrial sewing applications.
5. Maintenance and Durability
Why Do Best Industrial Sewing Machines Not Use Induction Motors in 2024? are expected to operate reliably with minimal downtime. While induction motors are durable, they often require more maintenance due to the wear and tear on components like brushes and bearings. This maintenance can lead to increased costs and interruptions in production. Servo motors, in contrast, have fewer moving parts and often feature brushless designs, reducing the need for regular maintenance and extending the motor’s lifespan. This reliability is crucial in an industrial setting where machine downtime can significantly impact productivity.
6. Flexibility and Adaptability
Industrial sewing machines are used for a wide range of tasks, from stitching delicate fabrics to sewing thick, heavy materials like leather. The motor driving the machine must be adaptable to these varying demands. Induction motors are less flexible when it comes to quickly changing operating conditions. Servo motors, however, can easily adapt to different tasks, providing the necessary power and speed adjustments on the fly. This flexibility is another reason why servo motors are preferred in industrial sewing machines.
Conclusion
The choice of motor in industrial sewing machines is driven by the need for precision, efficiency, and adaptability. While induction motors have their place in many industrial applications, they do not meet the specific requirements of the sewing industry. Servo motors, with their superior speed control, energy efficiency, torque consistency, and adaptability, are the preferred choice for industrial sewing machines. Understanding these differences can help manufacturers and operators make informed decisions when selecting the best equipment for their needs.